A Comprehensive Guide
to Cap Manufacturing
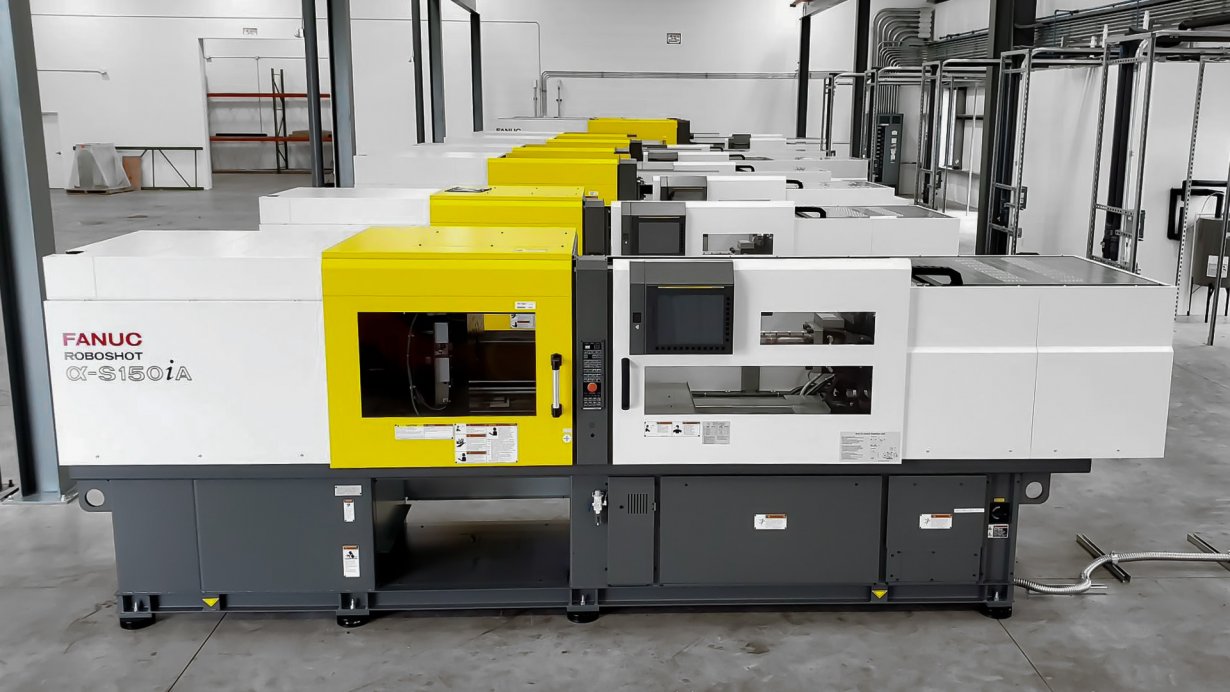
Fundamentals of Plastic Cap Manufacturing
The journey of creating a plastic cap begins with selecting the appropriate materials. High-density polyethylene (HDPE) and polypropylene (PP) are preferred choices due to their strength, flexibility, and chemical resistance. These materials are easily moldable and suitable for a variety of products, from beverages to personal care items.
The injection molding process
Injection molding is the cornerstone of plastic cap production. The process involves:
- Melting the plastic
- Injecting it into a specially designed mold
- Allowing it to cool and harden
- Ejecting the finished cap
This method ensures rapid production, consistent quality, and high output.
Expert Cap Mold Design
Designing an optimal cap mold requires attention to several factors:
- Ensuring a secure seal that is easy to open
- Incorporating tamper-evident features
- Allowing for air release during molding to prevent defects
- Integrating cooling channels for faster production cycles
- Strategically placing gates and runners for efficient plastic flow
Advanced Cap Molding Techniques
To stay competitive, manufacturers continually seek improvements in their cap-making processes. Key innovations include:
- Creating multi-cavity molds for increased production
- Utilizing robotics and automation for handling, quality control, and packaging
- In-mold labeling to streamline the production process
- Employing hot runner systems to maintain smooth plastic flow
Vasantha's Cap Manufacturing Expertise
We recently excelled in a challenging project for a major beverage company. Vasantha developed:
- A unique 96-cavity mold with advanced cooling channels
- An efficient hot runner system for better material flow
- An automated quality inspection system
- A robotic system for efficient cap organization
The outcome was a 30% increase in cap production, a 15% reduction in material waste, and defect rates below 0.01%.
Future Trends in Cap Manufacturing
The future of plastic cap manufacturing is poised for exciting developments:
- Adoption of eco-friendly materials for sustainability
- Integration of NFC chips or QR codes for traceability and consumer engagement
- Reducing plastic usage without compromising functionality
- Embracing Industry 4.0 with IoT sensors and data analytics
These advancements not only enhance efficiency but also contribute to environmental sustainability. Companies are exploring innovative designs for eco-friendly caps that are easily recyclable or biodegradable.
Conclusion
The seemingly simple task of making plastic caps involves a complex and dynamic process. From material selection to advanced mold design and high-tech manufacturing methods, there is always room for innovation. Companies like Vasantha are pivotal in meeting evolving customer demands and promoting sustainability. Their expertise in mold creation and technological advancements make them leaders in the packaging industry.
For brand owners and manufacturers, upgrading your cap production can significantly enhance your packaging. Vasantha's proficiency in mold making can give your production line a competitive edge. Reach out to Vasantha today to elevate your plastic cap manufacturing with cutting-edge, sustainable solutions.
Author: Gandham Rajini Kumar