The impact of
conformal cooling
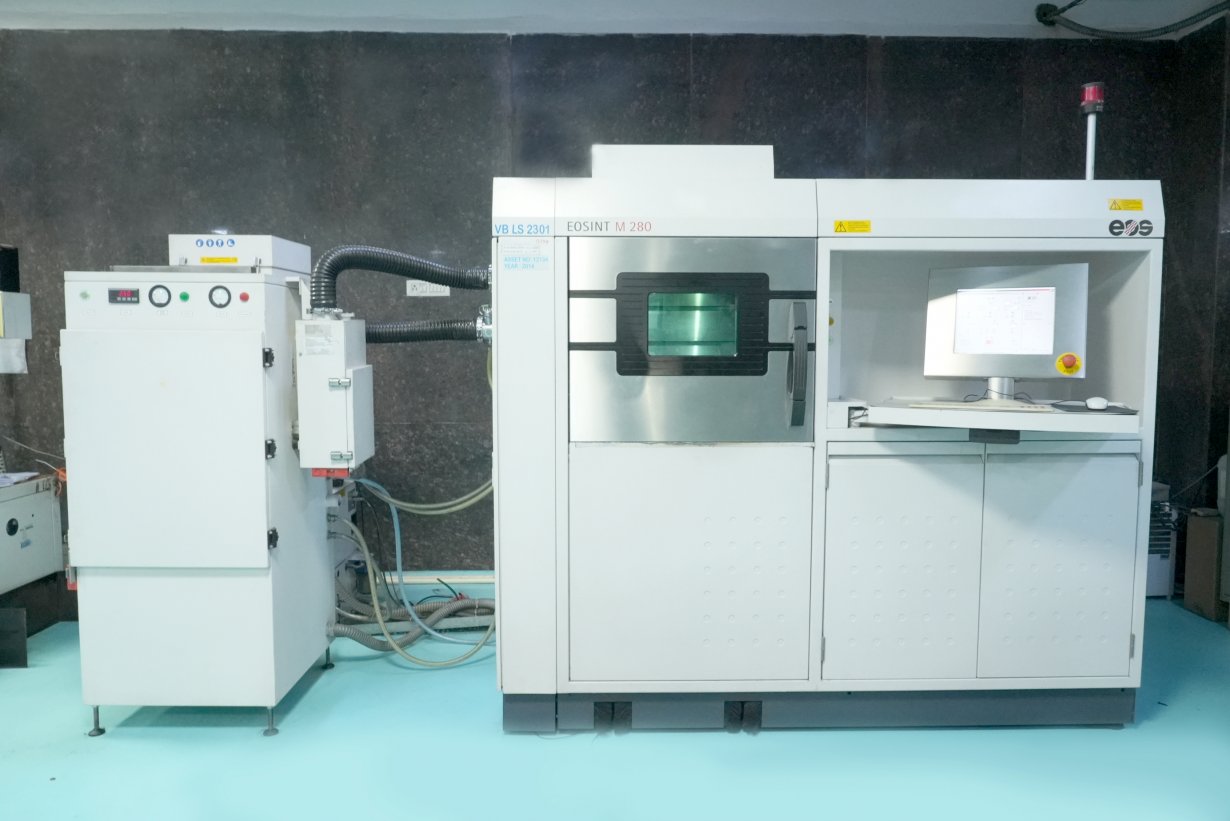
Why conformal cooling
Conformal cooling is used because it outperforms conventional cooling methods in terms of cooling speed, part quality (less warpage), process efficiency, and cost. With conformal cooling, cycle times are typically reduced by 10 to 40%, and sometimes even more than 40%. It also addresses the limitations of conventional cooling by providing uniform, effective cooling of complex part geometries.
Where to use conformal cooling channels
Conformal cooling is ideal for plastic parts with complex geometries (parts with thin walls and intricate features) that are difficult to cool evenly. Uniform cooling minimizes the chance of part defects in these complex designs. Conformal cooling is also ideal for parts that have: difficult-to-reach spots, curves, bends.
Common topologies of conformal cooling channels
a) Conformal cooling channels with basic topology: The spiral shape is one of the simplest and most common basic topologies for conformal cooling channels. Besides spiral, the linear shape (zigzag type) is an- other popular option for the topology of conformal cooling channels. It must be noted that as compared to the spiral type, the zigzag shape has many sudden turns that increase the pressure drop, thereby slowing down the flow rate and consequently drop the cooling efficiency.
b) Meshy-topological conformal cooling channels: The applicability of spiral conformal cooling channels reduces as the complexity of the geometric shape of the part increases. Compared to spiral conformal cooling channels. The two main characteristics of meshy topological CC channel systems are the complex topology and the non-uniform diameters of cooling channels. Consequently, the flow distribution and pressure drop are the critical design features one should optimize while designing a meshy-topological conformal cooling system
Benefits of conformal cooling channels in Injection Molding
The advantages of conformal cooling inserts are numerous:
1) Reduced Cycle Times: The cooling phase is typically the most time-consuming phase of the overall injection Molding cycle. Conformal cooling reduces the cooling time and, therefore, reduces the total cycle time.
2) Better Quality Parts: Because conformal cooling causes more uniform Mold cooling, it produces fewer Molding defects and less part warpage. This uniform Mold cooling results in higher quality parts.
Limitations of conformal cooling channels in Injection Molding
Designing of Conformal cooling channels in a Mold is a highly specialized design feature where the designer need to be optimised the conformal cooling channels for the best and most efficient cooling hence it is a time consuming process in the Mold design phase. The conformal cooling channels are expensive as compare to straight drilled cooling channels intern conformal cooling channel Mold is expensive. Vasantha has been a pioneering in designing and manufacturing of conformal cooling Molds over 3 decades.
Manufacturing of Conformal Cooling Inserts
The correct way to achieve the optimised conformal cooling channels through Additive manufacturing. Additive manufacturing is an emerging technology that manufactures three-dimensional (3D) objects directly from digital models through an additive process, typically by deposition of metal materials.
Vasantha has state of art Direct metal laser sintering (DMLS) facility with German technology where the metal powder free of binder or fluxing agent, is completely melted by the scanning of a high-power laser beam. The resulting part has properties like the original later vacuum heat treated to get the desired mechanical properties. This capability allows the inserts of Mold to be customized and manufactured with cooling channels that will fit the shape of the Molded part, leading to more uniform part cooling.
How the conformal cooling channels are different from conventional cooling channels
The main difference between conventional cooling and conformal cooling is that conventional cooling systems are designed to cool the surface of the plastic as it is being Molded; whereas conformal cooling cools the internal cores as the plastic part is being Molded. Compared to conventional cooling, conformal cooling facilitates faster and more uniform cooling. Conformal cooling is also used to cool complex geometries through curved custom-designed cooling channels, whereas conventional cooling implements straight cooling channels. Conformal cooling is a great way to improve the quality of your plastic parts. It's also an energy-efficient and cost-effective process that can save you time and money in production.
DeMolding temperature of the part in produced by conformal cooling channels
Conformal cooling does not change the target part temperature after cooling. The change in temperature is based on the material and the design being Molded. What conformal cooling does is change the rate at which the part cools to the desired temperature.
Conclusion
As you can see, conformal cooling inserts are a true game-changer in the world of injection Molding, particularly for the production of plastic bottle caps. By embracing this technology, you can optimize cycle times, improve part quality, increase production efficiency, and contribute to a more sustainable packaging industry. So, why settle for conventional cooling methods when you can elevate your bottle cap production to new heights with conformal cooling inserts.
Authors: Gandham Rajini Kumar & Kotaiah